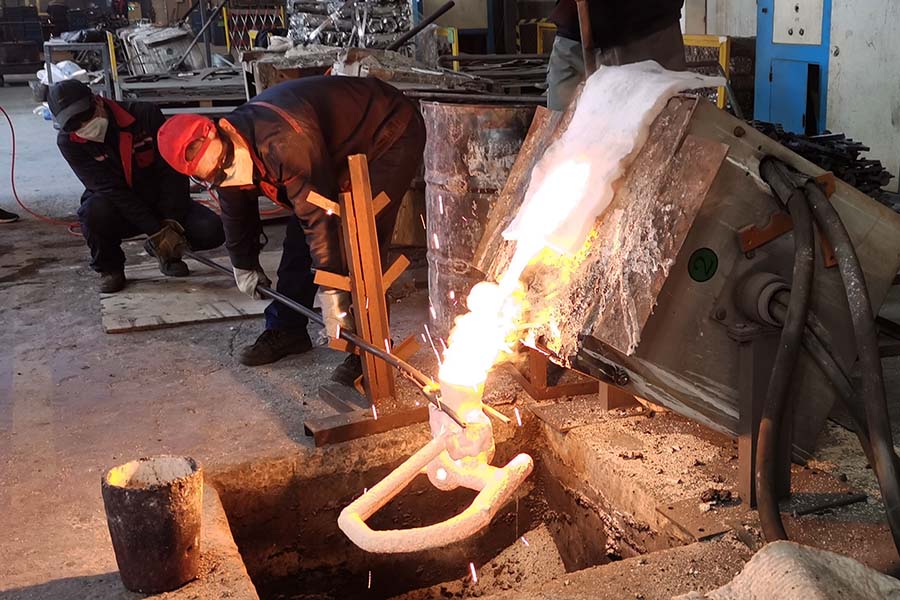
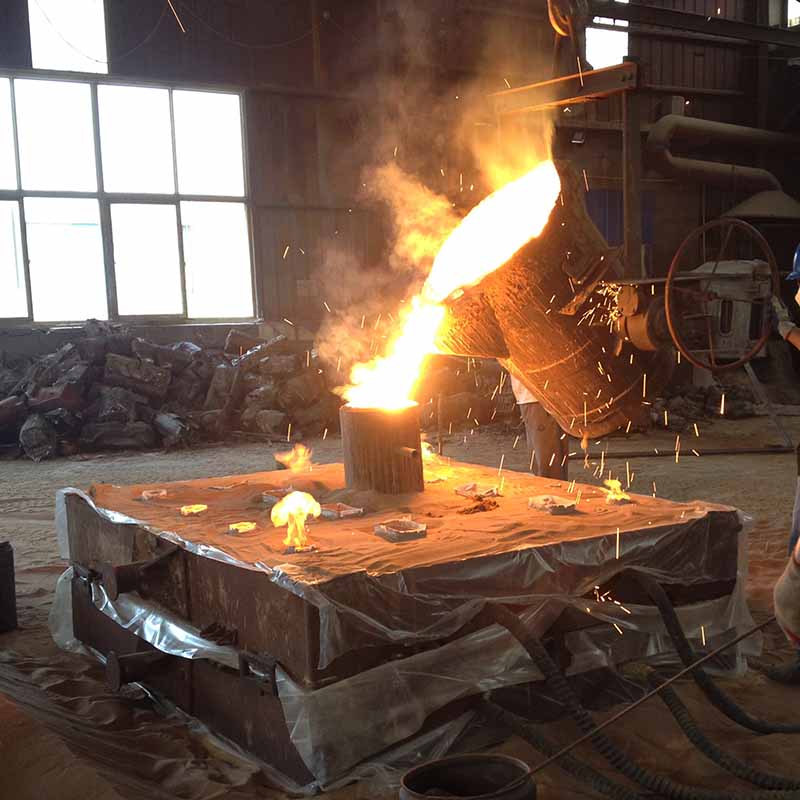
Az öntés az egyik legkorábbi ember által ismert fémformázási módszer. Ez általában azt jelenti, hogy az olvadt fémet egy tűzálló formába öntik, amelynek ürege az elkészítendő alakú, és hagyják megszilárdulni. Amikormegszilárdul, a kívánt fémtárgyat a tűzálló formából vagy a forma feltörésével, vagy a forma szétszedésével kiemeljük. A megszilárdult tárgyat öntésnek nevezzük. Ezt a folyamatot alapításnak is nevezik, és azt a modern gyárat, amely fémalkatrészek öntésével foglalkoziköntöde.
1. Az öntési folyamat története
Az öntési eljárást valószínűleg Kr.e. 3500 körül fedezték fel Mezopotámiában. A világ számos részén ebben az időszakban a rézbaltákat és más lapos tárgyakat kőből készült vagy sütött nyitott formákban alakították ki.agyag. Ezek a formák lényegében egy darabból álltak. De a későbbi időszakokban, amikor kerek tárgyakat kellett készíteni, az ilyen formákat két vagy több részre osztották, hogy megkönnyítsék a kerek tárgyak eltávolítását.A bronzkor (i.e. 2000 körül) sokkal finomabbá tette az öntési folyamatot. Talán először találtak fel egy magot a tárgyak üreges zsebeinek kialakítására. Ezek a magok sült agyagból készültek.Ezenkívül a cire perdue vagy elveszett viasz eljárást széles körben használták dísztárgyak készítésére és finom munkákra.
Az öntési technológiát a kínaiak nagymértékben továbbfejlesztették Kr.e. 1500 körül. Ezt megelőzően nincs bizonyíték arra, hogy Kínában öntési tevékenységet találtak volna. Úgy tűnik, nem voltak nagyszerűekismeri a cire perdue eljárást, és nem is alkalmazta széles körben, hanem több darabból álló öntőformákra specializálódott rendkívül bonyolult munkák elvégzésére. Sok időt töltöttek azzal, hogy a formát az utolsó részletig tökéletesítsék, így alighaa formákból készült öntvényen bármilyen befejező munkára volt szükség. Valószínűleg olyan darab formákat készítettek, amelyek gondosan illesztett darabokat tartalmaztak, számuk harminc vagy több. Valójában sok ilyen öntőforma került előrégészeti ásatások során Kína különböző részein.
Az Indus-völgyi civilizáció arról is ismert, hogy széles körben alkalmazza a réz- és bronzöntvényt dísztárgyak, fegyverek, szerszámok és edények készítésére. De a technológiában nem sok javulás történt. A varitólAz Indus-völgyi lelőhelyekről előkerült tárgyakról és figurákról úgy tűnik, hogy ismerték az összes ismert öntési módszert, mint például a nyitott öntőformát, a darabos formát és a cire perdue eljárást.
Bár Indiának tulajdonítható a tégelyacél feltalálása, nem sok vasalapítás volt nyilvánvaló Indiában. Bizonyítékok vannak arra, hogy a vas alapozása Kr.e. 1000 körül kezdődött Szíriában és Perzsiában. MegjelenikhogyvasöntésIndiában a technológiát Nagy Sándor inváziója idejétől, ie 300 körül használták.
A jelenleg Delhiben található Qutb-minár közelében található híres vasoszlop az ókori indiánok kohászati készségeinek példája. 7,2 m hosszú és tiszta temperöntvényből készült. Ez feltételezhetően aa Gupta-dinasztia II. Chandragupta időszaka (i.sz. 375-413). Ennek a kint, szabad levegőn álló oszlopnak a rozsdásodási sebessége gyakorlatilag nulla, és még az eltemetett rész is rendkívül lassú ütemben rozsdásodik. Ezelőször öntötték, majd kalapálták a végső formára.
2. Előnyök és korlátok
Az öntési eljárást széles körben használják a gyártásban, számos előnye miatt. Az olvadt anyag a formaüreg bármely kis részébe áramlik, és mint ilyen, bármilyen bonyolult forma – belsővagy külső – öntési eljárással készíthető. Gyakorlatilag bármilyen anyag önthető, legyen az vas vagy színesfém. Továbbá a formák öntéséhez szükséges eszközök nagyon egyszerűek ésolcsó. Ebből kifolyólag próbagyártáshoz vagy kis tétel gyártásához ideális módszer. Öntési folyamatban lehetőség van arra, hogy az anyagmennyiséget pontosan oda rakják, ahova kell. Ennek eredményekéntsúlycsökkentést lehet elérni a tervezésben.Öntvényekáltalában egyenletesen hűtik minden oldalról, ezért várhatóan nincs iránytulajdonságuk. Vannak bizonyos fémek és ötvözetekamelyet csak öntéssel lehet megmunkálni, kohászati megfontolások miatt semmilyen más eljárással, például kovácsolással nem. Bármilyen méretű és súlyú öntvény készíthető, akár 200 tonnáig is.
Azonban a méretpontosság és a felületi minőség normálhomoköntési folyamatsok esetben nem lenne megfelelő a végső alkalmazáshoz. Ezen esetek figyelembe vételéhez néhány speciális öntvényolyan eljárásokat fejlesztettek ki, mint a présöntés, amelyek részleteit a későbbi fejezetek ismertetik. Ezenkívül a homoköntési folyamat bizonyos mértékig munkaigényes, ezért számos fejlesztés irányul rá,mint például a gépi öntés és az öntödei gépesítés. Egyes anyagoknál gyakran nehéz eltávolítani a benne lévő nedvességből adódó hibákathomok öntvények.
3. Öntési feltételek
A következő fejezetekben a homoköntés részleteit láthatjuk, amely az öntés alapfolyamatát reprezentálja. Mielőtt belemennénk a folyamat részleteibe, meg kell határozni néhány szókincs szótárátmegfelelő.
Lombik– A formázólombik az, amely érintetlenül tartja a homokformát. Attól függően, hogy a lombik hol helyezkedik el az öntőforma szerkezetében, különféle neveken emlegetik, például húzás, megbirkózás és pofa. Fából készültideiglenes alkalmazásokhoz vagy általánosabban fémből hosszú távú használatra.
Húzza– Alsó formázólombik
Megbirkózni– Felső formázólombik
Pofa– Háromrészes fröccsöntéshez használt köztes formázólombik.
Minta– A minta a végleges objektum másolata, amelyet bizonyos módosításokkal kell elkészíteni. A formaüreg a minta segítségével készül el.
Elválasztó vonal– Ez a választóvonal a homokformát alkotó két formázólombik között. Osztott mintában ez egyben az elválasztó vonal is a minta két fele között
Alsó tábla– Ez egy általában fából készült tábla, amelyet a formakészítés kezdetén használnak. A mintát először az alsó deszkán tartják, homokot szórnak rá, majd a döngölést a vontatásban végzik.
Homokkal szemben– A formázóüreg belső felületére szórva kis mennyiségű széntartalmú anyag jobb felületminőséget biztosít az öntvényeknek
Formálóhomok– Ez a frissen készített tűzálló anyag, amelyet a formaüreg készítéséhez használnak. A kívánt eredmény eléréséhez megfelelő arányú kovasav és nedvesség keveréke, és körülveszi amintát a forma készítése közben.
Hátsó homok– Ez alkotja a legtöbb tűzálló anyagot, amely a szerszámban található. Ez használt és égetett homokból áll.
Mag– Üreges üregek készítésére használják öntvényekben.
Kiöntő medence– Egy kis tölcsér alakú üreg a forma tetején, amelybe az olvadt fémet öntik.
Spure– Az a járat, amelyen keresztül az öntőmedencéből az olvadt fém a formaüregbe jut. Sok esetben szabályozza a fém áramlását a formába.
Futó– Az elválasztó síkban lévő átjárók, amelyeken keresztül az olvadt fém áramlását szabályozzák, mielőtt azok elérnék a forma üregét.
Kapu– A tényleges belépési pont, amelyen keresztül az olvadt fém belép a formaüregbe.
Virágfüzér– Az öntőforma üregében lévő magok alátámasztására a szelvényeket használják, hogy gondoskodjanak saját súlyáról és leküzdjék a metallosztatikus erőket.
Hideg– A hidegrázás fémtárgyak, amelyeket a formába helyeznek az öntvény hűtési sebességének növelése érdekében, hogy egyenletes vagy kívánt hűtési sebességet biztosítsanak.
Felszálló– Ez egy olvadt fém tartály az öntvényben, hogy a forró fém visszafolyhasson a formaüregbe, amikor a fém térfogata a megszilárdulás miatt csökken.
4. Homokforma készítési eljárás
A tipikus homokforma készítésének eljárását a következő lépések írják le:
Először egy alsó deszkát helyeznek a formázóplatformra vagy a padlóra, így a felület egyenletes lesz. A húzóformázó lombikot fejjel lefelé az alsó táblán tartják a húzórésszel együttmintát a lombik közepén a táblán. A minta és a lombik falai között elegendő távolságnak kell lennie, amely 50-100 mm nagyságrendű. Száraz homokot szórunk ráa tábla és a minta nem tapadó réteget biztosít. Frissen elkészített, megfelelő minőségű fröccsöntő homokot most a húzóba és a mintára öntik 30-50 mm vastagságban. A húzólombik többi része azteljesen feltöltve a tartalék homokkal, és egyenletesen döngölve, hogy tömörítse a homokot. A homok döngölését megfelelően kell elvégezni, hogy ne tömörödjön túl keményen, ami megnehezíti a gázok távozását,se túl laza, hogy a forma ne legyen elég erős. A döngölés befejezése után a lombikban lévő felesleges homokot egy lapos rúd segítségével teljesen lekaparjuk a lombik széleinek szintjéig.
Most egy szellőzőhuzallal, amely egy 1-2 mm átmérőjű, hegyes végű huzal, szellőző lyukakat készítenek a húzóban a lombik teljes mélységéig, valamint a mintán, hogy megkönnyítsék a gázok eltávolítását. öntés közbenmegszilárdulása. Ezzel befejeződik a húzás előkészítése.
A kész húzólombik most az alsó táblára van gördítve, így a képen látható minta látható. Egy slick segítségével megjavítják a minta körüli homok széleit, és ráhelyezik a minta bordás felét.a húzási mintát, dübelcsapok segítségével igazítva. A húzófülke tetején lévő cope lombik a csapok segítségével ismét egy vonalba kerül. A száraz elválás homokot szórjuk az egész felületre és a mintára.
A mintától kis távolságban, körülbelül 50 mm-re található egy csapszeg a kivezető járat készítéséhez. Ezenkívül szükség esetén az emelőcsapot megfelelő helyen tartjuk, és ehhez hasonló frissen elkészített formázóhomokota húzóerőt a támasztóhomokkal együtt szórjuk meg. A homokot alaposan döngöljük, a felesleges homokot lekaparjuk, és szellőző lyukakat készítünk a fészekbe, akárcsak a húzásnál.
A kivezető csapot és az e felszállócsapot óvatosan ki kell húzni a lombikból. Később a kiöntő medencét levágják a csap teteje közelében. Az ütközés el van választva a húzástól és az esetleges laza homoktól a megbirkózás és húzás felületéna húzóerőt fújtató segítségével fújják le. Most a kapocs és a húzóminta felét kihúzzuk a húzótüskék segítségével, és a mintát körbeütve kissé megnöveljük a formaüreget úgy, hogy aa formafalakat nem rontja el a visszahúzódó minta. A futószalagokat és a kapukat óvatosan a formába vágjuk anélkül, hogy a forma tönkretenné. A csúszófolyókban és a penészüregben talált feleslegben vagy laza homokot fújjákel a fújtató segítségével. Most a paszta formájú burkolóhomokot az egész formaüregre és a futószalagokra visszük fel, ami jó felületi minőséget biztosít a kész öntvénynek.
A száraz homok magot egy magdoboz segítségével készítik el. Megfelelő sütés után a képen látható módon a formaüregbe helyezzük. A koponyát a húzóra cseréljük, ügyelve a kettő egymáshoz igazítására acsapok. Megfelelő súlyt tartanak a pálcán, hogy az olvadt fémöntés során a felfelé irányuló metallosztatikus erőt biztosítsák. A képen látható forma most kiöntésre kész.
Feladás időpontja: 2020-12-25